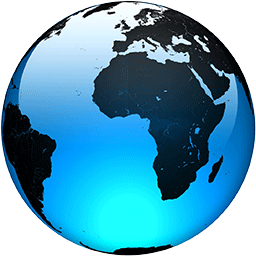
Under the skin: We need to torque about Audi's new drift tech
The Audi RS3’s Drift Mode can send almost 1300lb ft of torque to just one rear wheel
The forthcoming new Audi RS3 comes equipped with a new Torque Splitter rear-axle torque-vectoring system that does away with rear differential gears and replaces them with two ‘wet’ clutch packs.
The downside of a conventional differential is that it allows one wheel to spin if it loses traction, and in powerful cars that becomes a problem. The traditional solution is a limited-slip differential (LSD), which does just that: reacts if one wheel begins to spin by limiting the difference in the speed of rotation between left and right wheels. These can be controlled either mechanically or electronically.
Audi’s new Torque Splitter is a complete departure from its earlier systems in that it places no differential gears in the rear axle at all. Instead, a pair of bevel gears transmit the drive through 90deg, and these are flanked by two electronically controlled clutch packs running in oil. Each pack has its own controller and both are overseen by a modular vehicle dynamics controller (MVDC), which is like an orchestral conductor overseeing an entire group of chassis systems.
In the RS3’s case, the MVDC not only synchronises the two Torque Splitter control units but also the adaptive dampers and the individual torque control to the wheels. Sensors measuring longitudinal and lateral acceleration, steering angle, the throttle position and the yaw angle (the rotational angle of the car), the last of which is crucial to the torque-vectoring system. Many of these sensors exist already for engine and stability control systems, and all the data is used to control the Torque Splitter.
You might have already noticed that this Magna-supplied system bears an uncanny resemblance to GKN’s Twinster system (as used by the most recent Ford Focus RS and others). What both have in common is the basic arrangement of two clutch packs and a lack of differential ‘spider’ gears, but there’s one crucial difference. The system in the Ford has a fractionally higher final drive ratio on the rear axle drive to create the ‘over-speeding’ needed to send more torque to the rear than the front for drifting. When that’s not required, the torque is reduced to the rear by slipping the two clutches.
Audi has taken a different approach. Undisturbed, its system has a 50:50 torque split front to rear; and when more torque is needed at the rear for drifting, torque to the front is reduced. In the RS Torque Rear mode used for drifting, it continually varies torque to the front to keep the car in balance and can send 100% of the torque to the outside rear wheel, if only for a fleeting moment. At the other extreme, Comfort/Efficiency mode, it prioritises the front by slipping the rear clutches.
In other driving modes, increasing the amount of torque to the outside wheel in a corner can have the effect of reducing understeer and increasing agility. By apportioning more torque to the inside wheel, it can also reduce oversteer.
*Ford resorts to torture*
EVs aren’t known for carrying big payloads, but Ford’s forthcoming E-Transit van has undergone what the factory calls ‘torture testing’ to make sure that it can. As well as being subjected to temperatures of more than 40deg C and -35deg C (which is pretty standard fare for most cars these days), the E-Transit carried full loads almost 8500ft up on Austria’s Großglockner High Alpine Road.
*READ MORE*
*Clash on the 'pan: Torque-vectoring hot hatches face off *
*Under the skin: why torque converters are coming back from the dead *
*New Subaru BRZ launches with more power and torque*