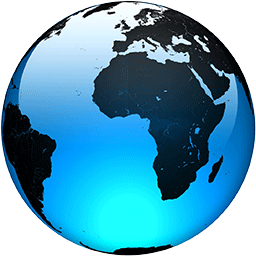
What the car factory of the future might look like
ABB, one of Europe’s largest robot manufacturers, believes radical new production methods are coming
A radical reshaping of automotive production lines, to include flexible manufacturing cells, robotic guided vehicles and automated parts warehouses moved to trackside, are the key to making electric cars affordable, Europe’s second-biggest maker of robots, ABB, believes.
ABB is pushing a radical new production system that abandons the traditional assembly/trim line, with its dozens of sequential assembly stations, in favour of multiple flexible manufacturing cells between which vehicles and parts bins are hauled on trolleys by automated mobile robotic vehicles.
Rethinking production to drive manufacturing costs down will compensate for the high cost of essential componentry in electrics, and is emerging as a key pivot point in automotive manufacturing, believes ABB.
“OEMs have got to reduce the price of battery-electric cars and that means more efficient factory operations,” said ABB global powertrain group manager Patrick Matthews. “The velocity of change in electrification technology right now is unbelievable and the EV transition is the main catalyst.”
*For Autocar Business webinars and podcasts, visit Autocar Business Insight*
ABB has commissioned research into the extent to which electrification will be introduced into the world’s car plants and predicts that 86% of European car output will be EVs in 2035, with the comparative figures for Asia and North America 86% and 45% respectively. With 13 years until 2035 (that’s just 1.5 model cycles in car industry terms), the industry is under pressure to make this changeover sooner rather than later.
ABB uses the initialism HSFS (Highly Standardised Flexible Solution) for the system, which it has been working on for a few years, and which has gained partial traction with at least two plants – one in Europe and one in the US – adopting the new way of working in a limited number of sections of the factory; in one case, a body-panel pressing plant.
“We are having conversations with many car makers who are looking for expertise on how to organise the shift to manufacture of electrified cars. This is a big challenge for them,” said Joerg Reger, ABB’s managing director of automotive robotics.
Automotive industry consultant Peter Wells of Cardiff Business School agrees there is a need for car plants to find new ways to build electric cars and believes automation companies like ABB are “pushing on an open door” as OEMs grapple with implementing major changes in their manufacturing operations.
“The push for more flexible assembly systems is ongoing,” said Wells, “and is well suited to battery-electric cars as the core platform [including battery pack, motors etc] stays much the same.”
Wells is referring to the possibilities of spinning multiple body variants off a skateboard-type chassis platform built around a standardised battery pack, and occupying less factory space than is typical today.
Audi demonstrated a version of the flexible cell-manufacturing system to the media in 2018, as part of a proposed ‘Industry 4.0’ rethink that links smart automation equipment to high-power data processing and artificial intelligence.
In a fully implemented version of ABB’s HSFS system, the body-in-white construction and final assembly would be organised into robotic cells operating flexibly, with some cells capable of multiple operations.
There might even be two cells operating side by side completing the same procedures, if the process is sufficiently complex and time-consuming to warrant doubling up. In a conventional plant, that would be highly unusual.
A key change to the traditional way of working would be to break away from the standardised ‘tact’ time, typically one minute in a high-volume car plant. “It is possible to split a one-minute operation into two 30-second operations, and maybe changeover tools, and add an extra step into the process,” said Reger.
Parts and modules to feed into the assembly cells would be stored in the assembly building within easy reach of automated guided vehicles and parts would be picked into a complete component set, which would follow the car on AGVs as it moved between manufacturing cells.
If ABB’s calculations are correct, the system could reduce manning in factories, which would feed into a reduced hours-per-vehicle figure – a benchmark for factory efficiency established for decades.
“This is the big challenge for OEMs to get overall costs down to compensate for the high price of components like lithium ion battery cells, and make electric cars more affordable,” said Matthews.
The man-hours for a medium-sized electric car is currently stabilising at around 10 hours, compared with the combustion-engined equivalent of 25 to 30 hours.
Nissan, for example, has stated its new Leaf is a 10-man-hours car, while the Tesla Model 3 is also understood to be a 10-hour car. For comparison, that is even faster than a low-cost small car, like a Nissan Micra, which is in the 12- to 15-hour range.
Volkswagen boss Herbert Diess has said VW will have to target 10 hours for future electric models, a huge efficiency increase for a company that currently takes 30 hours to build the ID 3 at its Zwickau plant, and is targeting a reduction to 20 hours.
Diess has said Wolfsburg, VW’s main plant with a capacity of at least 800,000 cars, will have to become much more efficient to survive the onward march of electric cars, which has caused unease with labour unions.
“If OEMs compensate for the high cost of componentry in electric cars with more automation, the risk is significant labour unrest,” said Wells.
The man-hours figure is a complex calculation and takes into account all the staff employed in a production plant, so workforce reductions – especially in non-frontline positions like warehouses – can make a significant difference to productivity.
Increasing off-site assembly of modules can have the same effect, but BEV battery packs are seen as a strategic component that an OEM should remain in control of.
“But it is proving very difficult to automate the production of the individual modules, with intricate wiring and small componentry,” said Matthews.
“And we are now having the battery pack built in the final trim and assembly plant,” added Matthews. “We never had that with combustion-engine cars. That brings more complexity into the plant and that’s also where robotics can help.”