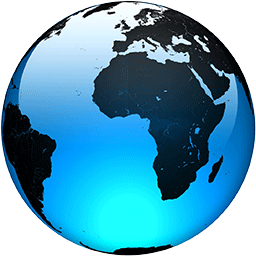
ForTwo to 4x4: How Smart factory became home to Ineos Grenadier
In 12 months of hard graft, Ineos has upgraded Smart’s Hambach factory for production of its Grenadier off-roader. We drop by
Things can happen fast in the car industry, but rarely do they happen this fast.
You’ve probably heard the story by now. In 2016, rueing the demise of the Land Rover Defender and Jaguar Land Rover's decision to replace it with something more haute-automotive, chemical engineering billionaire Sir Jim Ratcliffe, while in the pub, sketches the outline of a ‘spiritual successor’ to the famous off-roader.
The difference is that Ratcliffe isn’t dreaming. Four years later, the newly formed Ineos Automotive company had physical prototypes, an incipient manufacturing chain of command and, most importantly, somewhere to actually build the finished product. Just 18 months after that, in the here and now, it’s almost time to start full-scale production. And all this against the backdrop of you know what.
The factory is what cements Ineos as a serious entity and is why we’re now in eastern France, not far from Strasbourg. While the idea that Ineos was able to buy Mercedes-Benz’s Smart-manufacturing Hambach plant in December 2020 and simply begin building Grenadier off-roaders is a nice one, it’s also nonsense.
The factory’s 1000-strong workforce – the majority of whom are veterans, having stuck around since the initial Smartville staff intake of 1998 – is highly dependable. And the brand-new paint shop – which was part of a €470 million upgrade that Mercedes only recently lavished on the plant in anticipation of full-scale EQA and EQB electric crossover production and is where enormous emu-feather brushes sweep dust from freshly minted bodies – is state of the art.
The Grenadier will even use the same lines as the Smart cars, but therein lay the problem for Ineos’s manufacturing team when it gained the keys to the place (at the infamous expense of a much-anticipated new-build plant in Bridgend, South Wales). The Grenadier is five metres long and weighs 2600kg; attempting to build one – and, Ineos hopes, eventually more than 30,000 annually – on lines designed for something half as long and a third as heavy would result in carnage. So what exactly has happened to give this remote factory an unexpected new lease of life? Quite a bit. Ineos has already spent €50m on Hambach and is currently in the PT01 stage of its manufacturing plan. That stands for Production Try-out One, which is when the raw processes are put in place without any time constraints.
By now, explains industrialisation director Erik Torseke, most of the truly arduous work is done. In the bodyshop, where panels are spot- welded (4068 welds for the steel floor and shell, 368 for the aluminium doors and bonnet) and glued together, Mercedes’ 250 robots were removed, modified, then fitted with new heads before being put back into place.
That was some undertaking, but the fine-tuning is almost as taxing. Right now, many robots are running in ‘ghost mode’, where they eerily complete their task in mime. They will run through the motions tens of times, until the movements are perfectly calibrated, before any panels for customer cars are handled. Even before this, all 23 stations involved in the bodyshop assembly process – the entire floor, basically – have been computer modelled in 3D to nail the choreography.
The Grenadier bodies are then transferred via a sky tunnel to the building where the new paint shop resides. It’s uncomfortably warm, quite bright and, for now at least, superbly clean. The process here starts with corrosion protection, with PVC-based sealant applied by colossal robot arms that take a moment to measure up the squared-off, naked bodyshell but then attack it with fantastic precision, darting in and out of windows with centimetres to spare.
Some 3.7kg of sealant (about 120 metres’ worth) is applied in the 300 seconds a body spends at the station. Two base coats and a top coat later, it’s ready for the general assembly line in another area of the plant.
It’s in GA that most of the work to ready Hambach for Grenadier building has taken place. Achieving PT01 status in this part of the facility has involved removing, modifying and strengthening 75 overhead carriers. The fact that these will need to wield 2.6-tonne cars has also necessitated reinforcements to the building structure itself, particularly the roof.
The ‘skillet’ floor conveyors, adjustable through six heights so as to make the completed-byhand jobs of fitting the glass, interior and all other addenda easier for staff, have also been reinforced and enlarged. The stations that conduct the difficult eight-bolt operation of marrying the body and the chassis have been extensively modified. The chassis – an old-school ladder-frame design with beam axles from tractor specialist Carraro – has required an entirely new sub-assembly area.
Here, the six-cylinder BMW engine (diesel or petrol), ZF automatic gearbox and Tremec transfer case are fitted to the chassis. Naturally, drive is sent to all four wheels, and the Grenadier can be optionally fitted with electronically locking axle differentials. A centre differential, manually lockable via the low- range gearstick, comes as standard. Compared with an average Smart, the Grenadier’s rolling chassis is a monstrous, almost dystopian device.
In all, reaching PT01 included 23 simultaneous development projects taking place across all 133 assembly stations on the combined lines, with 20 suppliers involved, and it has all happened in the past 12 months.
Part of Ineos’s success has been to assemble a crack team of manufacturing experts. Torseke was a director at NEVS before joining Valmet Automotive, the Finnish firm that for years made the Boxster and Cayman for Porsche. CEO Philippe Steyer has worked in operational roles for Mercedes, often at Hambach, for 20 years. Stefan Bruhnke, who heads up quality control, is another ex-Mercedes man.
Inheriting cutting-edge kit meant originally for EQA production has also helped, and most likely it’s this (along with Hambach’s proximity to suppliers) that prompted Ineos to abandon Wales in favour of France.
While many of the factory’s processes in themselves are at the sharp end of modern mass-market manufacturing, the Grenadier remains a straight-forward prospect. By Torseke’s admission, the most advanced element of the construction is the casting that sits within the rear door, onto which the spare wheel is mounted. It’s an idea that Mercedes pioneered on the latest G-Class and makes the area more robust. The Grenadier is otherwise a rudimentary body-on-chassis affair, like the original Defender. The difference is that spot welding and particularly the automation of the bodyshop are a world away from the processes used to build the Defender, which even in 2016 – the final year of production – involved hammers and spanners to some extent.
The job now for Torseke and co is to push through to PT02, which will involve another 130 prototypes being built, on top of the 130 made during PT01. Vehicle development will also continue during this time, with 1.1 million miles anticipated.
It’s during PT02 that Hambach will accelerate to the operational speed necessary for the Grenadier venture to be commercial.
That 300-second cycle time will eventually become quite rigid. And after that? Then it’s time for customer cars, which should be in the hands of the first owners by September. What sort of people those customers will be and how they will choose to use their Hambach-made Grenadiers remains to be seen.
-Smartville-
Daimler-Benz’s trailblazing €450 million Hambach plant opened in 1997. It was known as Smartville, because of the numerous suppliers that operated on site, resulting in exceptionally low vertical integration in the production.
Only around 10% of the total number of production steps were completed by Smart (30% is more typical in the car industry), but this approach worked because of that supplier proximity, with components delivered almost directly to the production line. It meant that Hambach could exploit the just-in-time manufacturing principle to maximum effect, and in some cases components were delivered just in sequence – that is, in the correct order for assembly, with customer- specification data shared outside of Smart.
Because the site has its own railway station, finished cars could be moved on almost immediately, too, so the level of dormant inventory at both ends of the production line was – and remains – minimal.