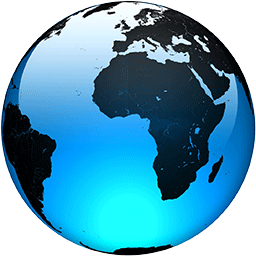
Appetite for destruction: how cars are crash tested
Euro NCAP’s crash tests have revolutionised vehicle safety. We visit the Thatcham test facility to find out how
To be reminded why their job is so necessary, the engineers who crash test cars at Thatcham Research need only glance at the Rover 100 stored at the organisation’s Berkshire-based site.
Its front end has concertinaed in the 40mph frontal offset crash test (other examples were subject to side and pedestrian impacts), but more shocking is how the impact energy has travelled to the cabin, buckling the car’s windscreen pillars. Inside, the occupant survival space has been severely reduced, while the steering wheel has been forced up towards the dummy driver’s head.
The Rover was among the first vehicles to be crash tested by the then new vehicle safety organisation Euro NCAP (the letters stand for New Car Assessment Programme) in 1997, or 25 years ago this month. In 2012, Thatcham Research became one of its accredited test facilities; today, Euro NCAP is based in Belgium, but it was actually a UK initiative conceived by the Transport Research Laboratory. The UK government quickly got behind the new programme, as, shortly afterwards, did the EU.
Worryingly for owners of the model, Euro NCAP awarded the Rover 100 just one star out of the four then available (today, the maximum is five). Even the best performers in the inaugural round of tests, the Ford Fiesta and Volkswagen Polo, earned just three stars. The results sent shock waves through an industry that had grown used to crash testing its new cars against only basic legislative requirements, keeping the results to itself and its customers in the dark. The fallout was quick and dramatic. Euro NCAP was and remains a voluntary scheme, but just five months later the Volvo S40 became the first four-star car for occupant protection.
Encouraged by manufacturers’ and consumers’ response, in 2000 Euro NCAP introduced one of its toughest tests to date: the side-impact pole test, in which a car, mounted on a platform, is pulled sideways into a pole. “It’s the toughest crash test because the pole is a like a knife,” Matthew Avery, director of research at Thatcham, tells me when I visit the test facility. In 2001, the Renault Laguna II was the first car to achieve the Euro NCAP’s new, maximum five-star rating, thanks to its impressively stable structure, pretensioner seatbelts and head airbag. The result encouraged more car makers to raise their game.
In 2007, Euro NCAP was encouraged to raise its game when, inspired by Volvo’s whiplash protection system introduced on the S80 in 1999, it began testing whiplash performance using seated dummies mounted on a sled. By 2009, Euro NCAP could claim there had been a 65% reduction in injuries among those travelling in a five-star car compared with those travelling in cars manufactured before the programme was introduced.
Since 2009, we’ve become used to cars achieving four or five stars. Not that the road to success is without the occasional pothole. Just last year, the facelifted Renault Zoe achieved a big fat zero. Explaining the shock result, Euro NCAP said: “The new Zoe offers poor protection in crashes overall, poor vulnerable road user protection and lacks meaningful crash avoidance technology, disqualifying it for any stars.”
Ordinarily, Euro NCAP wouldn’t test a facelifted model like the current Zoe, partly because it’s busy testing all-new ones (around 35 each year) and partly because its test protocols are changed every two years and significantly updated every five (the next update is 2025), so comparisons are unhelpful. It made an exception because Renault said the Zoe was radically different.
For some years, Euro NCAP crash tested cars into an offset deformable barrier, a soft-nosed structure that replicates the front of another car. A movable version, called the mobile progressive deformable barrier, replaced it in 2019. Both measure the ‘aggressivity’ of the test vehicle. Simply, a barrier that is too deformed after impact suggests the test car’s structure is too stiff, causing more crash energy to be transferred to the rest of the vehicle. Alternatively, if the barrier is barely marked, the test car is absorbing too much energy. “We encourage manufacturers to make large vehicles such as SUVs less rigid,” says Avery. In 2015, the full-width barrier crash test, which had previously been withdrawn, was reintroduced as a means of testing occupant loading.
If engineers at Thatcham are inspired to carry on their work by the sight of the buckled Rover 100, they should also be inspired by Thatcham’s Honda Jazz, tested in 2017. Granted, the Honda’s front end is crushed, but that’s impact absorption at work. More important, its windscreen pillars are unscathed, while deployed side airbags hang limply from its roof. “You can see the steering wheel angle is unchanged,” says Avery. “Much of the crash energy has been absorbed by the front end of the car. Although it was a frontal offset crash test and not a side-impact test, the side airbag has inflated. It’s why deleting it from the facelifted Zoe was so bad.”
The organisation’s most recent major test update was 2020, which Avery describes as a “breakthrough year”: “From the accident studies we do and data including RAIDS [it stands for Road Accident In-Depth Studies] that we receive, we noticed that more people were being killed and seriously injured in the nonstruck side of a car. Often, the cause was the way occupants interacted with the driver. It led us to recognise the fitment of centre airbags in new cars. We will continue to demand higher safety levels because our science and knowledge are constantly growing and we know manufacturers can do more.” On that point, in 2025, Euro NCAP protocol is likely to introduce a new automated driving assessment.
Avery and his engineers are acutely aware of their responsibility to produce results that are consistent and repeatable. Accordingly, before and after testing, they take detailed measurements of every car and the location of dummies, which must be fitted precisely. Twice a year, all cars crash tested at Euro NCAP facilities are delivered to the Brussels headquarters so that car makers can scrutinise them.
“We encourage them to share their insights,” says Avery. “However, we do ask them not to bring tools. Some have been known to take away parts of the cars for inspection.” So the crashed cars can never be repaired and returned to the road (yes, this has happened, although not with Euro NCAP cars), all of the wrecks are then crushed. For millions of drivers around the world, that sacrifice has not been in vain.
*The crash tests*
Euro NCAP’s tests probe four key areas of vehicle safety: Adult occupant protection, child occupant protection, vulnerable road user protection and safety assist.
*Front offset crash test: *This Euro NCAP staple was conceived in response to research from the 1960s that found most frontal crashes were partial rather than full width. As a result, just one side of the car absorbed all the impact energy, leading to greater cabin intrusion and to the occupants’ bodies twisting.
*The hyper G: *Propelling a test car mounted on a sled at up to 40mph into a crash barrier within a very short distance is the job of Thatcham Research’s Hyper G, a pneumatically powered ram. Operating at a pressure of 120 bar, the ram pole extends just 1.2 metres. A series of computer-controlled brakes at one end of it allows engineers to finely control the ram pole’s acceleration and deceleration in order to achieve consistent and repeatable results.
*Active safety testing*
Passive safety is what engineers at Thatcham test, but Euro NCAP also requires active safety systems to be assessed. For this work, the engineers go to the former RAF base at Upper Heyford. It was here that Thatcham developed a test protocol for car-to-car automatic emergency braking. It followed it up with protocols for pedestrian and cyclist AEB, and lane support function. “We always push for the implementation of a new safety system if we know a manufacturer has cracked it,” says Thatcham’s Matthew Avery.
For AEB tests, engineers remotely drive the subject car towards a remote-controlled sled carrying the GST (Global Soft crash Target), an object assembled from sections of absorbent material that resembles a white Ford Fiesta. For cyclist and pedestrian AEB testing, lifelike forms mounted on small remote-controlled sleds are used. The next generation of tests will focus on systems that monitor the driver’s eye openings and look for signs of distraction.
*Meet the dummy family*
Thousands of motorists owe their lives to crash test dummies such as Thatcham’s. Unfortunately, like those at other Euro NCAP test facilities, most are Hybrid 3 models based on morphologies dating back to the 1950s. Another problem is that their sensor capabilities haven’t kept pace with crash testing. One, the EuroSID 2, can measure side chest compression, but there isn’t an ideal solution. “We have yet to have a dummy we can use in all crash scenarios,” says Matthew Avery.
The new Thor-50M takes a step closer to that goal. During our visit, Thatcham displayed one produced by Cellbond, a maker of passive safety products. Claimed to be the most lifelike dummy yet, Thor has been adopted for the Mobile Progressive Deformable Barrier test. Multiple sensors enable it to measure soft tissue, abdominal and pelvic trauma as well as brain, spine and neck injuries.