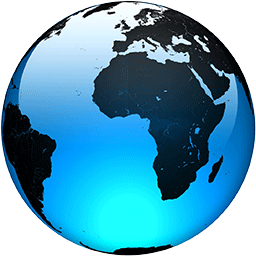
The Knowledge: how the future of car manufacturing is shaping up
Ineos has bought the Smart factory from Mercedes-Benz
In the latest edition of Autocar Business Live, we chat to industry experts about the latest trends in car factories
Disruptors are demonstrating that legacy car manufacturers don’t necessarily have all the answers and that includes where car factories are concerned. When it comes to how to build a car, the big OEMs are ploughing billions into expanding their existing facilities, but there are alternatives. The microfactory is not a new concept but has become popular recently with start-ups such as Arrival, while Ineos has forged a different path and effectively taken over the old Smart Hambach factory, using the brownfield site to build the new Grenadier.
Erik Torseke, director of operations and supply chain for Ineos Automotive, and Peter Wells, pro-dean of public value at Cardiff Business School, joined us for an in-depth discussion about the future of car manufacturing.
*What is a microfactory?*
Peter Wells: “Well, a microfactory is actually more than just a place where you manufacture cars. We conceived this as microfactory retailing and something that combines a manufacturing operation and the retailing operation, but on a very small scale. So it's more than just a factory. It's actually a business strategy and a whole new business model which allows smaller, new entrants to penetrate what has traditionally been an industry dominated by economies of scale.”
*Did Ineos look at microfactories for the Grenadier?*
Erik Torseke: “No, we did not. I mean, what we were looking at was either greenfield or brownfield and we had gone quite far with the greenfield option when the opportunity came to acquire the plant from Mercedes. But with the volume that we're looking at and with the implication of the supply chain, there are significant benefits to produce all of the cars in one place.”
*What’s driving this change in some areas of the factory business model?*
PW: "Everything comes together here. There's been some really interesting developments in terms of the ability to use digital technologies in the manufacturing space that allow a smaller scale and flexibility. So that's been important in terms of balancing materials, better use of more lightweight materials, different process technologies, and this has really opened up a space where in the past really everything had to be steel. We've moved away from that already. And that opens up many more opportunities for more innovative attitudes. “The market potential can be tapped by smaller operations without having to throw everything in an all-or-lose bid to try and get a bit of market share. I think one of the things we looked at with the microfactories was: what is the expansion route for a business? If you have to go in for a 300,000-unit-per-annum factory, that means you've got to sell a lot of cars very quickly.
“And you know, Ineos will face this for a new brand. You've got to convince a lot of customers very quickly. Alternatively, with a more incremental manufacturing strategy, which opens up different geographic spaces bit by bit, you can expand your manufacturing in line with the market. You don't have to put so much in all at once.”
*What sort of size are we talking about here for the microfactory to be a viable option?*
PW: “I think a microfactory can work at 5000 units per annum. I mean, we started this research looking at many of the often British small-scale manufacturers. We went to Ferrari, we went to Lotus, we went to all of these kinds of manufacturers to see how they worked at that level.
“And a lot of the innovations there really relate to how they work with their customers and how they generate customer loyalty. That linkage between the factory and their customer base was really important.
“In terms of scale, we actually envisage this moving over time without the dealership network. Once you've started manufacturing cars and once you’ve started to put out there, we saw the microfactory also operating as a remanufacturing facility. So as the cars needed to be refreshed and returned, the factory itself could move over from not just producing new to being more and more involved in remanufacturing and generating income streams beyond the necessity to sell cars.
“That was a key issue that has been really interesting in this period. We just had the issue with supply constraints: all of a sudden, manufacturing is profitable. Why is that the case? Well, actually, typically, the market suffers from chronic overproduction, that the collective aspect of every vehicle manufacturer means there's too many cars coming onto the market. They get discounted. Profitability is very low and depreciation is very high. We want to escape that trap whilst also introducing more environmentally sustainable technologies. And we thought the microfactory approach was one way to do that.”
*Why isn’t it taking off then?*
PW: “Well, we see elements of that breakthrough going on all the time. And bear in mind that the collective idea of microfactory retailing came from looking at many different companies. What I see is that even some of the biggest companies are adopting elements of this business model.
“I'll give you a classic example. Volkswagen is investing heavily in battery recycling and is talking about retaining ownership of the cars over one, two, three, even four leasing cycles and then bringing the cars back to be recycled in their own facilities. This circularity of the business model is one of the things we proposed in this microfactory approach.
“Obviously, you've got companies like Arrival, who finally have got some big money behind them, and that's the key. You still need major investments to break through into this industry. What we're proposing is so radically different that I think it's hard for investors to be convinced that it's a safe place to put that money. But we will see more and more of it.”
ET: “One of the challenges in this model is the enormous amount of parts that go into the building of a vehicle. If you have a general assembly where you have maybe 130 stations in a plant with a takt time of a few minutes. In a microfactory, you have longer takt times, which means that you have staff that have to remember many, many more things to do. That makes it a challenge when we do ramp up vehicle production or building small series [of vehicles].
“If you're looking at building some 60,000 vehicles and divide them into micro plants, I would say it would be quite difficult from our point of view. From an Ineos point of view, it was never anything that we were looking at because we're looking at scale. It's easier to do that with one plant with capacity.
"But I think for mass-produced vehicles, I think it's quite tough just because of the logistics challenge that you have then to ship parts to several plants all over the world rather than doing it to one place.”
PW: “It's interesting you moved into that brownfield site - as Tesla did in California, of course, in order to really ramp up their production. But, a while back, Hyundai was looking at maybe investing in a plant in the UK. All the regions started competing for that possibility and here in Wales we had just one place that might be suitable for a large automotive assembly operation of the type that you're describing – just one. So those greenfield sites are actually really rather precious.
“One interesting element of the underlying logic of the business model with the microfactories is that you actually could move into a much smaller-scale facility, a pre-built facility, with relatively little requirement in terms of additional new floor space. And that made it attractive.”
*Is the supply chain important?*
ET: “One of the difficulties of the automotive industry is that for roughly a €1 million to €2 million, we can build a show car. You can give the impression to journalists that you have a vehicle that is more or less ready to go into production but where in reality you haven’t even done 5% or 10% of what's needed to make the vehicle. And then, of course, you're talking about the challenges of putting it into production.
“We somehow associate that [putting it into production] with building plants, body shops and paint shops and so on. But actually, if you look at it, it's probably a bigger effort: it's building a supply chain. So it's a huge investment in supplier tooling and finding new suppliers that are then willing to work with us as a company. I think that's a lot of it.”
“You're looking at somewhere around 200 suppliers that you have to set up. You have to ensure that each of those suppliers can build the parts, in the quantity or quality and that they meet all of the requirements of an auto industry. If you have the incumbent tier one suppliers, they may be less interested in supplying [a start-up]. I think one of the big challenges that I think we have been very successful within Ineos is to build a very, very strong supplier network. We brought them in very, very early as partners in the development.”
*We’re hearing about relations breaking down with some suppliers and some manufacturers. How much does that feed into this idea of mega-factories versus microfactories?*
PW: “Yes, you can achieve economies of scale through a platform-based approach to product design, shared componentry and so on. But then you also get those occasions where a key component fails, which you've used across several vehicles across your product range, and then you've got to recall them all because of the same problem.
“We see this increasingly going on at the moment. One of the concerns for vehicle manufacturers has been to appreciate that to some extent you need to mitigate against that kind of risk because there's reputational damage as well as a financial cost. And so the whole kind of mega-factory approach, which depends upon those very tight economies of scale within one or two suppliers, is always going to be vulnerable.
“We've seen that with the war in Ukraine for some key areas of supply, because there's only one or two suppliers. And those linkages back into European factories have been broken. So this question of supply, resilience and vulnerability has certainly become more important in recent times.”
*Ineos has announced plans to build an electric car in the future. Will that change your manufacturing plans?*
ET: “From a technical point of view, not really. The good thing is the paint shop that we have is actually made to paint electrical vehicles. The ovens for an electrical vehicle paint shop need to be different from an ICE vehicle.
“You have a different marriage when you do an electrical vehicle. So instead of marrying the drivetrain, you now marry the battery.
“Then, of course, the other thing we have is batteries. You have to figure out whether you make your own battery packs or outsource.
“But otherwise it’s similar. You still have the steering wheel, four doors - there’s still seats.”
PW: “One thing I'd be interested to pursue a bit further is this question of recycling, because that’s the other side of this story of the transition towards electric vehicles. So the manufacturing operation itself is obviously key, but what are we going to do with all of these batteries when they're finished with? I did mention earlier that Volkswagen has already got a pilot facility running to dismantle those battery packs: that suggests to me that they see value in this and that they want to co-locate, as far as they can, with the battery manufacturing operation because they'll be feeding those materials back into the operation.”
*What will manufacturing look like in 20 years’ time?*
ET: “If you go back to when the Ford Model T started manufacturing, they kind of revolutionised how those vehicles [were made]. If you look at how we're building vehicles today compared to what they did with Model T, it's [largely] the same.
“As long as the vehicles have some kind of doors and closures, seats in them and a body, we will have to figure out some way to mass produce these.
“Maybe there are new materials. Maybe this way we can reduce the takt time by using carbonfibre or similar. Or maybe we have pre-painted panels to get away from the paint shop. It's possible. General assembly will still continue to be somewhat of a labour-intensive activity.
“Then again, will people own cars? Is it transportation you're buying rather than the vehicle? And if that's the case, then you probably change everything.”
PW: “The future of the industry is digital, largely Chinese and much smaller.”