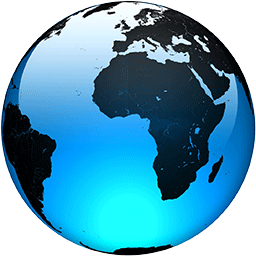
The business of battery testing: How EV hardware is made safe
Millbrook Proving Ground hosts a series of facilities to conduct crucial – and often dramatic – tests for cells
If you ever take an electric car for a drive, spare a thought for the high-tech, high-voltage battery under the floor, because prototypes of it will have been subjected to two years of technical tortures before being declared safe for production.
In detail, that battery will have been vibrated, squeezed, pressurised, dropped from a height, over-charged with electricity, frozen, heated, barbequed at 800deg C and even, god forbid, penetrated.
The fact is that the battery of every EV has to undergo dozens of extreme tests, specified under United Nations Regulations ECE 38.3 and 100.3, before being cleared for production. And there's an engineering centre of excellence in the UK – at the Millbrook Proving Ground in Bedfordshire – where British expertise and facilities are developing the next generation of batteries exactly to these specifications.
“It's purely down to safety and the safety case,” said Phil Robertson, Millbrook’s global activity manager of electrification. "Individual cells, modules and packs have to undergo and pass a wide range of abuse tests before they can be signed off for production and sold in a finished car.”
The starting point is the lithium ion cells themselves, officially classified as hazardous goods because of the risk of fire. They have to be tested to ECE R38.3, which declares them safe for transport and day-to-day handling, before the next stage of ECE R100.3, which validates the safety of modules and the packs fitted into cars. These packs are the batteries that manufactures quote in their car specs as 40, 60, 80kWh or whatever.
Generally, tier-one cell chemistry manufacturers do the legwork to validate to ECE R38.3 standard, which includes extreme environmental testing, such as hot/cold cycles over a range of -40deg C to 70deg C to simulate air cargo transportation at altitude (cold) to a hot climate; prolonged vibration over a range of 7Hz to 200Hz over a three hour period; and shock to simulate an accident in transit, with forces ranging from 50g to 150g, such as being dropped off a forklift truck or falling off the top shelf in a warehouse.
Once a manufacturer knows its chosen tier-one cell design is compliant with ECE R38.3, it incorporates it into modules and battery packs, and testing of these falls under UN ECE 100, which uses very similar g-forces, temperature ranges, vibration frequencies and pressures.
“The testing has to be repeated at module or pack level,” said David Prigg, manager battery tests at Millbrook, "because if you change the environment for the cell, then you have to repeat it for modules and packs.”
Millbrook has a significant R&D lab for ECE 100 testing, called, naturally, the Battery Test Facility, with 12 high-tech stainless-steel test-cell chambers, operational since late 2018. Into these, modules and complete built-up battery packs – the skateboard type designs in most EVs, typically rated between 40kWh and 120kWh – can be loaded for testing.
Two more test cells are being built to go operational in February 2023, and Millbrook has calculated that it has enough space nearby to extend to up to 70 chambers in future.
Each test cell is double-skinned, insulated and features fire-protection equipment, a blow-out roof air vent in case of explosion, a 500kW power supply and a data-logging network that can handle dozens of thermocouples and other instrumentation for monitoring battery-pack performance.
Elements of the test-cell designs are shared with units established at the Mercedes-AMG Formula 1 team's site at Brixworth, where Prigg once worked.
Test cells are temperature and humidity-controlled and backed up by a DC battery charged by off-peak power and housed in an adjacent building to provide round-the-clock electrical energy to power 12 batteries through charge/discharge cycles.
Each battery pack is subjected to this process 24/7 for two years to gain ECE 100 approval, which simulates a 10-year service life. Millbrook has 10 of its 12 chambers fully booked on this work, hence the need for more capacity.
An important part of the testing is to over-charge the battery to simulate incorrect operation of the power electronics system and explore if the battery fails under this abuse. “What happens to the cells in that situation? Testing is the only way to find out,” said Prigg.
Despite the rapid progress in validation and testing of battery packs, in these early years of EV technology, there are still gaps in the testing knowledge. There's no scientifically robust method of accelerated-wear testing on batteries, as there is for ICE.
During ICE testing, for example, components like pistons and crankshafts can be overstressed and the engine run at higher temperatures to speed up wear and cut development time, but there’s no such a methodology for EV battery packs yet.
“There’s a lot of work going on to try to understand what's possible to develop accelerated wear on battery packs,” said Prigg, “because reducing the amount of time to gather all the data will be genuinely revolutionary.”
As well as the Battery Test Facility, Millbrook has two other battery testing areas on its vast 665-acre site – and for reasons that will become clear, they're at remote locations, where destructive testing can be safely carried out.
First is the ‘penetration or nail test’, in which a sharp probe is pushed through the battery pack wall to breach the cells and initiate a fire by causing a short circuit and/or exposing flammable lithium to the air, promoting a thermal runaway in which multiple cells catch fire.
Currently, the nail test is manufacturer best practice, not mandated in ECE 100, but it's expected to be added in future.
Even more dramatic is Millbrook’s unique-in-the UK indoor petrol-fire simulation rig, which at first sight looks like a giant barbecue smoking shed.
A two-storey steel outhouse fashioned from shipping containers, this structure is designed to contain exploding battery cells when the battery pack is subjected to a fierce petrol fire.
This drama is specified in UN ECE 100 to simulate an EV crashing into the rear of an ICE car, resulting in petrol leakage and a fire under the EV. The battery must resist the fire for 2min 10sec— sufficient for vehicle occupants to exit a vehicle after a crash.
In the test, the battery pack is subjected to 800deg C heat from pans of burning fuel ignited underneath the battery pack.
During this roasting, super-heated battery cells give off hydrogen and can explode into the test building, constrained by the steel walls.
Not surprisingly, the roof of this test facility has already been replaced once in its four years of operation.
*Millbrook under new French ownership*
Millbrook is entering a new phase in its development, now under the ownership of UTAC and its CEO Laurent Benoit, with the goal of winning more business at the core of a group that specialises in vehicle testing, type approval, electric, autonomous and 5G technology development.
Benoit, a former Peugeot engineer, is now boss of a £172m-turnover business with 1300 employees (500 in the UK) at six test tracks and four test labs, the latter two US sites, one in Germany and another in China.
“Our target is to double our turnover in the next four years, and we're already seeing growth, especially in electric powertrains and connected vehicles,” said Benoit.
Thanks to the growing emphasis on EV powertrain development, UTAC’s business is already split about 50:50 with ICE development, with a further shift in that direction forecast.
Millbrook is the best known of the test tracks, and along with its Leyland Truck site and Test World in Finland was merged in June 2021 with UTAC’s historic base at Montlhéry and CERAM (formerly Simca’s test track) near Paris, backed by £68m of French private equity funding from Eurazeo. A brand-new hot-weather testing site in Morocco will open shortly.