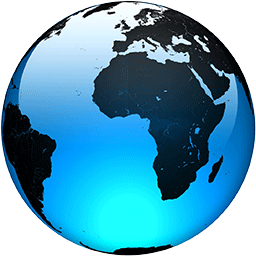
Under the skin: How carbon tubes can slash emissions
With the tubes are aligned vertically, there’s an electrical resistance across them horizontally
Nawa Technologies' system cuts complexity and use of materials for 900% extra strength
Nawa Technologies has been showing how versatile its carbon nanotube technology is for, ironically, reducing carbon emissions.
Its latest use of the technology, called Nawastitch, is a method of strengthening traditional carbonfibre to achieve a 900% increase in impact damage resistance while cutting weight by 20-30%.
Already in commercial use in sports bicycle wheel rims, the material is also aimed at producing tougher, lighter EV battery casings and hydrogen storage tanks for fuel cell vehicles. It can also be used inside fuel cells to improve performance and increase lifespan.
As well as cutting weight, the plan is to use the electrical conductivity of the material to turn casings into an integral heating element, helping to reduce the complexity of battery thermal management systems.
In addition to being a lightweight strengthening material, nanotubes make a good basis for the anode of lithium ion and other battery chemistries.
Nanotubes are known as vertical aligned carbon nanotubes, or VACNT for short. They are grown on a thin underlying layer (substrate), reach a height of between five and 100 microns (a micron being one-millionth of a metre) and resemble a molecular-scale forest of around 100 billion tubes per square centimetre.
Carbonfibre components consist of layers of woven carbonfibre fabric laminated together in layers using resin. A weakness is when the resin breaks due to impact damage or vibration and cracks form across those layers. Adding a layer of Nawastitch between the layers of carbonfibre mat ties them together and that’s where the extra strength comes from.
In practice, the nanotube layer is a thin film that can be handled in the same way as carbonfibre mat during manufacturing of components. Because it’s so thin, its weight is insignificant but it reduces the amount of carbonfibre and resin needed while also increasing the strength.
The material is being developed to replace the aluminium base and plastic superstructure of EV battery casings to make them stronger but lighter. Because the tubes are aligned vertically, there’s an electrical resistance across them horizontally, so if a current is passed through them, the material becomes a heating element.
The aim is to use that property to help manage battery temperature and potentially improve the range of EVs.
Nawastitch is also being used to make lighter and stronger compressed hydrogen storage tanks for fuel cell and hydrogen ICE vehicles. Tanks are at the lab testing stage now and are expected to be available to customers in 2024.
Nawa is also developing the use of its VACNT technology in hydrogen fuel cells as a base for the platinum catalyst material. The nanotubes lock the particles in position, preventing them clumping together over time, increasing the power and also the life of fuel cells by a factor of five.