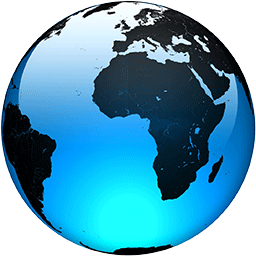
Why simulators are the future of engineering
MIRA’s Tom Lee shows Prior the future of engineering
Prior talks about how car development is hastened when virtual, and why that's good news today
I’m indebted to (and a little envious of) my colleague Richard Lane for his recent visit to the Ansible Motion simulator.
I’ve spent a good amount of time in simulators over the past decade – more than my colleagues, to the point that I’ve felt like I’m our sim correspondent.
They do have more visual impact in person than they do in photos for you, dear reader. If we drive a real prototype car, there will be shots of it on ice, in a desert or at a track, as it throws up snow or sand or is chucked sideways by a heroic test driver.
See a prototype car during simulated development and, no matter what it’s doing or where it virtually exists, it will always look like a big screen and some thick cables in a darkened room. Make that look exciting if you can. I suppose it’s like any driving.
Driving or racing is fun to do, and watching it is good too. But virtual driving? I like racing games, but they’re an acquired taste, less exciting than the real thing, so watching somebody else playing one must be even more acquired.
If actual racing is like drinking wine, watching somebody race a simulator isn’t even like watching someone else drinking wine. It’s like watching them pretend to.
But back to industry sims. Horiba MIRA, the test centre that until recently hosted our performance car road tests (inconveniently for us, they’re building a solar array on our handling track) has a new one.
It’s not from Ansible, rather VI-Grade, but the whole set-up, including a less advanced supplementary sim, has still cost it £4 million and incorporates the very handy ability to put an engine or drivetrain in a separate room and make it respond to real human inputs.
This is particularly good news. Most cars aren’t fully electrified, and getting hybrid drivetrains to behave well is evidently difficult. They stop-start, they shunt between motor and engine and they can take an age to get going or change gear as they try to make human demands match emissions-regulated response.
The ability to refine them in a lab where one can make adjustments rapidly, rather than having to pound asphalt in a prototype, will more quickly make better cars. And that’s just one of dozens of vehicle traits that sims can handle.
“Manufacturers have had to shift very quickly to new platforms,” says MIRA driven attributes engineering manager Tom Lee. “That takes away their brand DNA, and they have to redefine what that could be.”
So if you feel like we reached ‘peak car’ in terms of dynamics and drivability (and you wouldn’t be alone if you did), this rapid shift in vehicle engineering is why.
The old way of doing things – making cars a tad bigger, more efficient, faster, plusher and pricier each time – is over. Cars are so much more complex than those they replace that they’re no longer routinely better.
Steve Cropley recently found the Ford Kuga’s dynamics particularly disappointing for a firm that used to offer benchmark ride and handling. But the car was developed during the mid-2010s, when plug-in hybrids were still only a twinkle in engineers’ eyes.
So, depending on its powertrain, the Kuga weighs anything from 1526kg to 1859kg, and who knows how different the distribution of mass is between an ICE version and a PHEV?I bet Ford would handle the development situation differently today – much more of it virtually, before a real car ever turned a wheel.
“We’re a way off not needing [real] prototypes,” says Lee, concurring with Ansible boss Kia Cammaerts, “but our goal is to have all the development done here, so we’re only doing validation [with physical vehicles].”
Pics of development cars will be less exciting, then, but the end products should be better.