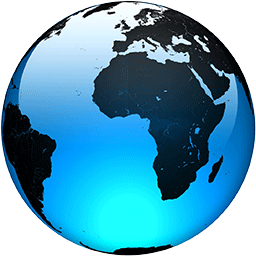
Aero testing the new Ariel Atom 4R in Catesby tunnel
Prior and Cropley tested the Atom with a series of sprint runs
Catesby is a 1.7-mile disused railway tunnel turned aero test facility - we help Ariel get some drag coefficients
If you need convincing that minimising aerodynamic drag is vital in cars, all you need to know is that above about 40mph, a car’s aero load is the main retarding force for its engine to overcome, exceeding stuff like mechanical drag and rolling resistance.
Since most cars can do much more than 40mph, another fact comes starkly into play: that aerodynamic drag rises as the square of speed. Double the speed and you need four times the power. Treble the speed and you need nine times the power.
A car that needs 40bhp to do 40mph needs around 360bhp to do 120mph. No wonder creators of both road and race machinery spend big money to keep drag as low as they can.
Yet even this is elementary stuff. A modern car also needs downforce for high-speed stability and on-rails cornering, plus more subtle diversions of its airflow into radiators and over wings.
Such essentials mostly add to drag rather than reducing it, so they need careful development. Chuck in the inconvenient fact that aero is invisible and you have a unique, gigantically complex puzzle that carries some of the biggest risks and rewards going.
These are all reasons that recently took an Ariel engineering group, and their latest Atom 4, to the unique Catesby aerodynamic test tunnel in Northamptonshire for a secret test session in which Autocar drivers were invited to participate.
Under test was the car’s minimal but carefully designed cockpit protection screen. The logic was clear: the Atom may be a car with a surfeit of power and performance, but at its easily attained high speeds, cockpit protection is vital.
Here was an opportunity to discover first hand whether its protection was as effective as required, plus what effect the screen design might have on the car’s drag factor and its lift/downforce.
On hand were Ariel founder Simon Saunders, Catesby tunnel manager Paul Roberts, me and Autocar colleague Matt Prior, plus a couple of Ariel’s technical specialists to analyse results from data loggers already fitted to the car.
The idea was that Prior and I – plus Ariel’s own technical expert, Kelvin Marshall – would do a series of coastdown tests in the tunnel, with and without screen, accelerating to 60mph, then coasting in neutral to 20mph and doing it again. The loggers would record variations in speed and time, assessing the effects by computer.
Prior and I both knew from experience how effective Ariel’s modest air dam ahead of the driver has always been at cutting turbulence around the driver’s head. Back in the 1990s, we were among the first to learn that a fist-sized flyscreen just ahead of the steering wheel made a surprising difference. But that was in an Atom 2 and now we’re up to the Atom 4R.
The first lesson at Catesby, which took minutes to learn, was about the effectiveness of the Atom’s latest cockpit screen. Without it, the 60mph-plus blast was hard to bear for more than a few hundred yards, even for bespectacled drivers like us. With the screen in place, though it looked small, Prior and I could each have driven 100 miles home.
And there were more lessons ahead. Catesby’s main boast is that it caters to the industry-wide need for repeatable, real-world aero testing.
Such conditions are difficult to achieve in conventional wind tunnels (where tethering systems intrude, wheels don’t spin, tyres don’t achieve their loaded shapes and engine exhausts and cooling systems aren’t active) or on open test tracks (where temperatures, pressures, gradients, variable road surfaces and weather intrude).
It’s true that designers nowadays confidently use CFD (computational fluid dynamics) to predict with great reliability how air flows over cars. Indeed, Catesby’s leading backer is Totalsim, a well-regarded CFD company. But car designers still have a strong demand for physical testing – which is where Catesby wins.
Which other venue could offer a straight and flat test track protected 365 days a year from wind, weather and prying eyes, with a perfect surface and no noise regulations to interfere?
Catesby provides all of this. It is a perfectly straight, 2.7km (1.7-mile) former Victorian railway tunnel, running through a confluence of rural hillsides south-west of Daventry in Northamptonshire.
Opened in 1897 as part of the Great Central Railway’s double-tracked London Extension, it was ‘retired’ by Dr Beeching in 1966, then sealed and fenced off until the early 2000s, when it came to the notice of Totalsim managing director Rob Lewis and his colleagues as they searched for a suitable tunnel.
They already had experience of aero testing in the world’s only other converted railway tunnel, Chip Ganassi’s shorter and semi-secret facility at Laurel Hill in Pennsylvania, although even before that they had intended to open a bigger, longer and flatter facility available to all comers.
“If you take away the usual variables in an aero test,” says Lewis, “you’re inevitably going to get a better result. From an engineering point of view, it’s common sense.”
Work began in 2017 on what was to become the world’s biggest aero test facility, comprising around 30 million Staffordshire Blue bricks but now relined for its entire length with plastic sheeting.
Its 8.2m width was bounded by Armco on both sides, CCTV cameras were installed all over, and a network of overhead fire extinguishers and lights was fitted. The whole project took over four years and unspecified millions to build (including £6.2 million from the government’s Local Growth Fund) and it also included resurfacing with Tarmac of the same quality as Silverstone’s grand prix circuit.
One of Catesby’s best claims to fame is that beginning an experimentation programme is quick, and so it proved. Ariel’s blokes arrived with the car’s data collection system already working. All we had to do was remove the screen and start driving.
For the likes of us, helmet-wearing amateurs in normal clothes, there’s a 60mph limit in the tunnel. Other users – properly kitted BTCC teams, Le Mans racers – are allowed much higher speeds, although the tunnel’s operators reserve the right to run risk assessments and frame different rules for different users.
It’s an eerie experience, driving the tunnel, with the lights arching over your head and all the car’s noise reflected faithfully back from the domed roof. There’s an echo too. Even a mile a minute feels fast at first.
I found myself wondering what it would be like at 150mph in an LMP1 car. On the other hand, the road is wide, an Atom 4 is ultra-stable and, of course, it accelerates like a rocket. Even though Prior and I may have strayed a smidgen further up the speed range than 60mph (who could resist?), it was still easy to do three runs in each direction, northerly at first towards a driver-operated turntable (essential, I would imagine, for big-bodied LM cars) and then southwards and back to the start.
Beyond the northerly turntable, we were told, was 60m of bat colony, its existence a condition of the aero tunnel’s planning approval. According to Roberts, the bats are impervious to sound, even LMP1 cars at full noise, as long as they are undisturbed in other ways.
Interpretation of the results – beyond the surprising protective qualities of the screen – took a while, but they were fascinating. “Our tests showed that the screen generates 100 Newtons of downforce, which helps shift the aero balance to the centre of the car. It reduces buffeting and directs air into the engine’s intake too, and also reduces drag. So we’ve had a win-win-win,” says Saunders.
“This fine level of testing wouldn’t be possible for us outside the tunnel. Improvements like this are repeated all over the car, and together they make a very direct and noticeable change improvement for occupants. So it has all been very well worthwhile.”
*Final results*