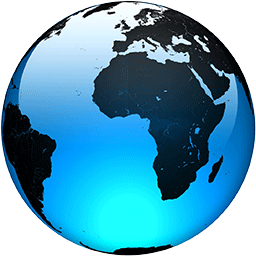
BMW's flexibility now the industry standard to survive EV reality
More are following the company's cautious decision to treat electric as just another drivetrain option
Just ahead of his elevation to the position of CEO at BMW in 2019, then production head Oliver Zipse spoke at an event at the Mini plant in Oxford about the need for caution when it came to EVs.
“Flexibility is key,” he told journalists. “If we predict the success of [the BMW] 3 Series, we can be pretty much spot-on. To predict electromobility is much more difficult.”
Five years later, BMW is reaping the rewards of its more circumspect strategy. In July, the company actually sold more electric cars in Europe than the global EV leader Tesla, according to market research firm Jato Dynamics.
But BMW’s EVs are even today still just adapted versions of combustion-engined models, built on the same production lines.
Back in 2019, BMW stood in opposition to the Volkswagen Group, which was about to show the first model based on its EV-specific MEB platform, to be built at a plant outfitted for just that platform.
Indeed, the ousting of Zipse’s predecessor Harald Krüger was widely attributed to his failure to provide clarity on BMW’s own EV strategy after becoming a pioneer with the well-liked but costly i3.
BMW gambled on a cautious approach. Rather than redesigning the car to unlock the potential of the electric drivetrain (for example by liberating more cabin space, as Volkswagen claimed), it offered electric as just another drivetrain choice.
“You won’t feel difference as a customer. You maybe will find 2kg here and 2kg there, but that is not relevant for a buying decision,” Zipse said back in 2019.
Fast-forward five years and not only is BMW is Europe’s number-two EV seller, but it also has buoyant profits, at €3.7 billion (£3.1bn) in the second quarter to the end of June, translating into a margin of 10.5%.
“Many years ago, we bet on the right strategy to be as flexible as possible,” Zipse said on the company’s second-quarter earnings call. “You're better prepared if you have ultimate flexible portfolio and an ultimate process competence to react to these things.”
This much cheaper strategy is now seen as the gold standard for companies as they recalibrate for a lumpier demand for EVs than expected.
“Car companies at the moment are forced to work with two three drivetrains: BEV, hybrid or ICE. What we see is that flexibility is very valuable,” said Ingo Stein, head of automotive at consultancy Bain & Company. “You can balance the demand shift much easier than a company that produces different cars with different drivetrains.”
In Europe and particularly the US, companies are shifting more of their production to hybrids after the expected EV boom hasn’t materialised at the speed first envisaged after Tesla’s original spectacular stock rise.
Hyundai, for example, is switching its planned new electric-only 'Metaplant' in Georgia, the US, to build hybrids as well to bridge what it calls the “chasm” to EV demand.
“We've seen very clearly a trend in the market demanding more hybrid, so we decided to be flexible and introduce hybrid into our Metaplant,” president and CEO Jaehoon Chang told investors late in August.
Hyundai is projecting to sell 1.33 million hybrids globally by 2028, up 40% on its previous plan. It also plans a rollout of extended-range electric vehicles (EREVs).
Ford is another looking for flexible options after delaying plans for an all-EV plant in Tennessee, the US, after cancelling its previously announced seven-seat electric SUV.
“You have to have a compelling product roadmap and you have to have very flexible manufacturing,” CEO Jim Farley said on the company’s second-quarter earnings call.
Ford’s van strategy has embraced that flexibility at its plants in Turkey, where the Transit Custom and related Volkswagen Transporter are built in plug-in hybrid, electric and diesel forms on the same line.
Plenty of other manufacturers have adopted the flexible approach too. Stellantis even builds a hydrogen fuel-cell version of its K-Zero line of mid-size vans (think the Vauxhall Vivaro) at its plant in Hordain, France, alongside electric and diesel versions.
Stellantis said this was done in accordance with its “ethical desire not to separate its electric and internal-combustion-engine businesses, to engage all its employees in the energy transition”.
Unplanned flexibility can be expensive, however, especially when a company was banking on EVs forming a greater portion of sales earlier in the cycle.
JLR, for example, announced earlier this year that it had increased its five-year investment plan from £15bn to £18bn after the slower-than-predicted EV take-up forced it to boost spending on 'flexible' platforms that allow ICE as well as electric powertrains.
The hike was “partly because we are having to invest more in keeping the parallel running of flex vehicles, BEV vehicles and ICE vehicles going for longer than we anticipated as the industry trend towards BEV globally starts to slow down from previous expectations,” CFO Richard Molyneux told analysts at the company’s investor day in June.
JLR is continuing to build ICE models at its Halewood plant, home of the Range Rover Evoque and Land Rover Discovery Sport, even after it begins production of EVs on a new platform.
JLR’s tardiness into the EV market is a good thing, the company believes. “Many competitors have placed their bets, done their investment, launched their cars and quite a few have regretted it. It's one of the advantages of being a follower rather than being first in the market,” Molyneux said.
Volvo meanwhile has been forced by customer demand to upgrade its XC90 large SUV and extend production at its plant in Torslanda, Sweden, after initially saying it would be replaced by the new electric EX90. It also will extend the life of other ICE and hybrid models even as it rolls out EVs on new platforms.
“In this transition period from an ICE world to a BEV world, we can temporarily have a broader product portfolio,” commercial chief Björn Annwall said at a recent investor event.
Car makers are having to commit to dedicated EV platforms as they seek to extract all the cost and technology benefits that come from dumping the multi-fuel approach.
BMW, for example, will next year launch the first model based on its EV-specific Neue Klasse platform, expected to be a SUV previewed by the X concept.
The company is investing €2bn in the new battery-making and assembly operations for Neue Klasse models at a plant in Hungary.
BMW hopes these EVs, with their promised 800V electrical architecture enabling ultra-fast charging, will be appealing enough to drive sales to the point they can sustain whole plants, but it remains a gamble.
Ultimately, companies are still dealing with the same unpredictable nature of the EV transition as Zipse highlighted back in 2019. Waiting for a long as possible to scrap profitable ICE models will help them navigate that.