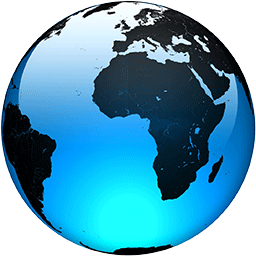
First new UK hydrogen fuelling hub open in 2024
Element 2 will open four refuelling sites over the next year
British firm Element 2 one winner of government's £8 million North-East hydrogen development fund
A plan to create a nationwide network of hydrogen refuelling stations has taken its first steps into becoming a reality as part of a £8 million UK government grant, with the first to open "early next year".
Initally, four stations will be built by British start-up Element 2 which will be publicly available to drivers of both HGVs (the government is targeting supermarket delivery trucks) and cars.
Although their main focus will be on commercial vehicles, and therefore locating these pumping sites at trick stops, this also means cars like the Toyota Mirai, Hyundai Nexo and new BMW iX5 Hydrogen will be able to use Element 2’s pumping technology.
The pumps will be built in the north-east of England, Element 2 CEO Tim Harper told Autocar, given the funding is to develop the Tees Valley Hydrogen Transport Hub.
The first will open “early next year” at Teesside International Airport. This will be to support fellow funding winner Ulemco, which will develop hydrogen-powered airport vehicles, such as aircraft tow trucks and runway sweepers.
Harper confirmed a further 30 pump locations will be identified and have plans in place by the end of the year. Element 2 is working with a range of forecourt operators and vehicle manufacturers, he added.
Last July, the firm announced its first two sites with planning permission approved, at Coneygarth on the A1 (near Northallerton) and on the M6 near Carlisle.
“The strategy is that we have the infrastructure first, ideally in place next year, before these vehicles arrive in numbers,” Harper said. “There's a wave of [commercial] hydrogen vehicles coming. It's a question of when, not if, and to be honest, with this funding, we now know the when.
“This funding gives us the seal of confidence, as it's public money that has gone through a lot of scrutiny before reaching us.”
Harper added that funding for “some of the other stations” has also already been secured.
As well as the two mentioned projects, a further £300,000 of funding will be sent to local colleges to support local workforce training as well as developing future talent.
This “further cements the Tees Valley’s status as the home of hydrogen”, according to the government.
“Hydrogen technology has great potential to decarbonise transport and help grow the economy,” transport secretary Mark Harper said.
“Today’s winners illustrate the expertise the Tees Valley has as a pioneer in developing hydrogen tech. This investment will provide a further boost to the economy, creating skilled jobs and apprenticeships across the North East.”
*Additional reporting by Will Rimell*
*Why hydrogen is important to the UK*
Skipton-based Element 2 has been building its business plan since 2019 and in the next few months will move to the operational phase with four sites underway, followed by 30 further locations either earmarked or under construction by the end of the year.
“Then we should be able to say to fleet operators that we have a national network with about 100 miles between stops, which in a vehicle with a range of between 300 and 400 miles isn't a problem logistically,” said Brendan Bilton, chief technology officer at Element 2.
“The important detail is that our refuelling equipment is compatible with car fuel cells, so we will be ready when fuel-cell cars come to the market. But recently we’ve adjusted our forecasts and brought forward demand from light commercials ahead of private cars."
Trucks and buses are the number-one priority for Element 2’s hydrogen, because the 600,000 trucks daily operating in the UK contribute 18% to road transport emissions.
There's also a better business case for refuelling stations focused on trucks and buses, since a truck typically consumes 50kg of hydrogen per day, a bus 20kg and a car just 1kg.
Given that 1kg of hydrogen currently costs £15 including 20% VAT (but no fuel duty), just 1000 trucks pivoting to hydrogen will generate £750,000 of revenue per day.
“We worked out early on [that] you can make good money out of this as long as you have enough hydrogen going through your pumps,” says Bilton.
Before the today-announced government grant, Element 2 had made rapid progress with a relatively modest £6.5 million of investment. Two further funding rounds totalling £100m will be launched later this year and ultimately investment is likely to hit £1 billion by 2027.
The hydrogen fuel cell has been tomorrow’s technology since the mid-1990s, but Carbon Zero policies have accelerated their introduction in heavy trucks, soon to be followed in light commercial vans and pick-ups.
Battery-electric technology will provide many solutions – Vauxhall’s Ellesmere Port plant is pivoting solely to electric van production, for example – but the range and speed of refuelling of fuel cells is attractive to some.
“From all we hear from operators, about 30% of operations, mainly urban work, can be met by battery-electric haulage. For other operations, it's the fuel cell that can replace the internal combustion engine,” said Bilton.
Tevva, the British start-up based in Tilbury, Essex, is selling a 7.5-tonne Hydrogen Electric model, combining a 5kg 350bar hydrogen fuel-cell range-extender with a 112kWh battery for 354 mile range, more than doubling the electric-only range.
American firm Nikola is planning to launch in Europe in 2024, while established truck makers like Iveco, Hyundai, Mercedes-Benz, Toyota and Volvo are also working on hydrogen technology.
Lower down the weight scale, Toyota is partnering with Ricardo using funding from the government’s Advanced Propulsion Centre to develop a fuel cell Hilux pick-up truck, with small-scale production planned at the Burnaston plant in Derbyshire.
Given that pre-pandemic UK sales of pick-ups were averaging 53,000 per year and light commercials around 300,000 per year, the opportunities to decarbonise with fuel-cell vehicles alongside BEVs are enticing.
To fulfill this emerging demand, Element 2 is concentrating its network on the UK’s 147 truck stops. It estimates that it needs 800 individual nozzles – about five per truck stop – by 2027 to provide comprehensive national coverage.
At its truck-stop sites, the hydrogen pumps will be located on their own forecourts, away from petrol/diesel areas. They will be fed by 40ft-long compressed-gas tanker trailers, towed from a central depot, decoupled from their tractive unit and parked alongside the pumps in a secure compound.
Safety follows ADR dangerous goods transport regulations, in use internationally in industry, which commonly uses compressed hydrogen stored in tanker trailers.
Element 2’s operation is focused on compressed gaseous hydrogen at 350bar, which Bilton said offers the best balance of efficiency and speed of filling. They could operate at 700bar, but the higher pressure causes heating of the gas during filling, which has to be offset by complex cooling systems that also incorporate periods of dwell, when pumping has to be stopped for 30 minutes or so.
Other operators have tried this higher-pressure hydrogen delivery but have found the complex on/off pumping and switching processes unreliable when not in constant use.
Distribution has been contracted to two specialist tanker companies, Reynolds Logistics and XPO Logistics, and although these trucks initially are diesel-powered, Bilton expects Element 2’s trucking operation to switch to fuel-cell trucks as early as practicable.
“Some people in the hydrogen debate are solely focused on a single issue: efficiency. But the bigger picture is more important: replacing diesel trucks with a cleaner, practical alternative.”
*Where does the Hydrogen come from?*
Element 2 has a hydrogen supply contract with chemicals giant Ineos, from its Runcorn plant on Merseyside, where H2 is a by-product of the chlor-alkili process, using electrolysis of aqueous sodium chloride (salt).
Because the process isn't based on hydrocarbons, it produces 99.97% pure hydrogen – essential to avoid damaging the catalyst inside a fuel cell.
According to trade association Eurochlor, which represents chlor-alkili producers, annual European production is 270,000 tonnes, equivalent to the output of a 2GW water electrolyser and equal to about 35% of Europe’s total hydrogen output. About 45% is used for fuel and 45% for chemical processing, with the other 10% waste.
Eurochlor describes this hydrogen as having a “low carbon footprint”, at 0.2-0.55kg CO2 equivalent per kilogram – 90% lower than hydrogen from fossil-fuel based processes.
More significantly, the emergence of a market for hydrogen as an “energy vector” will mean a commercial use for the 10-15% of output that's currently wasted because there's no demand for it.